Replacement of FG Wilson Woodward GCP 30 Generator Controller
Due to a long and successful working relationship with the client we were asked to quote for the supply and installation of replacement generator paralleling control panels for six generators currently fitted with FG Wilson paralleling control panels incorporating Woodward GCP30 controllers which are now obsolete.
The new control system would be designed to replace the existing six generator automatic paralleling control systems and incorporate all of the same facilities, plus some additional features which enhance the performance of the control system. The design of the new control system would be based upon ComAp IG-NTC-BB model controllers with an Intelivision 5 interface.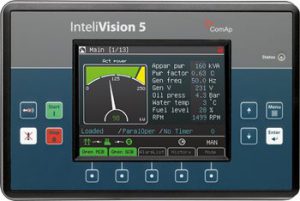
On receipt of the work being awarded to The Generator Company, a dedicated project manager was appointed ensuring that the project was afforded the attention it required throughout.
Preceding to any works being carried out, our project manager attended site to carry out a comprehensive site survey to understand the scope of works involved and finalise the work schedule for the project ensuring deadlines were met.
Following the site survey a programme of works was planned and completed. The upgrade of the control panels were scheduled to be replaced in sequence over a two week period to safeguard the critical nature of the services ensuring there was no down time and therefore no disruption or risk to the building infrastructure and daily operating procedures.
Prior to installation of the control panels the need to also replace and reconfigure the start marshalling circuit was identified. The current system recognised each pair of generators as one generator which meant the system required a minimum of two pairs of generators available to go on load. This system left the site vulnerable in that if one generators from each pair failed then the site would not be supported and be put at risk.
The start marshalling circuit was modified so that the generators would be identified as individual sets. Following the upgrade an assessment of site load was made proving that when a minimum of three sets were available the site would be supported.
The new Control Panels were assembled and tested at The Generator Company panel workshop over a 10 day period by our Senior Controls Engineer and shipped to site.
On commencement of works in week one, Generator 1A and 1B was taken out of service allowing our engineers to replace the control panels. Upon completion and commissioning of the works of 1A and 1B Generator 2A followed suit. Following the upgrade of the first three generators, they were tested using a reactive loadbank and put back into service ready for the upgrade of the final three generators the following week.
Week two saw the remaining 2B, 3A and 3B generators taken out of service and control panels replaced as per week one.
Following all control panel upgrades, all six generators were loadbank tested and commissioned by our Commissioning Engineer.
The final stage of the upgrade involved setting up the Power Management facility in the ComAp controllers; this facility is enabled when the mains fail and all six generator sets start and come on-line after a set period of time. Once site load is at the expected load two generators will shut down leaving the four other sets to support the site.
In the event of a generator failing one of the other sets will start to maintain the minimum requirement of four generator sets being run at one time. Should the site load continue to increase set number five would start then subsequently generator set six should it be needed. This is also the process when the load is decreasing i.e. generator sets will shut down as the site load decreases but will always maintain a minimum of four sets. This means that generator sets are only in use when they are required which in turn allows the client to meet their environmental obligations.
Following dedicated training The Generator Company left site with an extremely satisfied client. All relevant documentation and operating manuals for the new equipment was left with the client as well as reports on the successful commissioning of all equipment.