The Generator Company was contacted by the current main contractor for a global, multinational entertainment company to discuss if we could provide a solution to alleviate generator cooling issues that were occurring due to the layout of the existing machinery and plant on the roof area above the generator room at their offices in North West London, following recent building extension works.
Having worked with the end-client for over 10 years carrying out the generator service and maintenance and relocating their existing generator to roof level we were very familiar with the equipment and the current layout.
Following a site visit by our Project Manager who met with the contractor’s Construction Manager to assess the current site conditions and constraints, methods were discussed at how best to alleviate the cooling issues.
Subsequent to the site meeting our Project Manager recommended several solutions that would resolve the issues raised; one being to extend the ductwork to allow the air to disperse more evenly and to raise the outlet louvres dissipating the heat to prevent hot air recirculation between the inlet and outlet louvres. Unfortunately it was established that this method could not be undertaken as this type of extension of the ducting and louvres would obstruct the windows of the proposed new offices. We also had to take into consideration the issue of heat build-up due to the exhaust outlet and heat radiating from the exhaust silencers mounted on the roof directly below the proposed new air inlet louvres.
With the added challenge of the proposed new offices additional meetings followed both internally and with the main contractor, to discuss solutions of how best to position the new ducts and louvres; one to minimise the recirculation of the hot air discharge from the outlet louvres particularly on extended running and any days where high temperatures were experienced and two, not to obstruct the proposed new office windows.
On submission and approval of revised final drawings the decision was made by the end client to remove the roof from the existing penthouse louvre assembly and replace with an extension duct. Steel work was to be erected around the existing louvre, giving a new roof level with a screen wall attached to illuminate air recirculation from the existing generators on the roof area.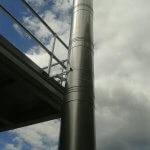
The existing exhaust outlet will also be raised to a level just above the new roof perimeter wall with an open terminal routing exhaust gasses away from the inlet louvres thus virtually eliminating the risk of exhaust gas recirculation. The proposed new generator exhaust flue will be routed vertically from the existing tail pipe section and secured to the new steel work. The flue will be terminated approximately 500mm above the top edge of the new roof screen wall with an open terminal to allow for the best dissipation of the exhaust gasses on discharge.
To significantly reduce the amount of radiated heat, we also proposed to undertake the lagging of the exhaust silencers and the associated interconnecting pipe work.
On the agreed project start date our engineers arrived early to attend a site safety induction followed by meeting and instructing the tower crane driver lifting the site box containing tools for the job onto the roof. Once the box was in position, the engineers could proceed with the removal of the roof of the existing penthouse louvre assembly and cover with a temporary tarpaulin to provide weather protection until the new extension was ready to be attached. The operation of the standby generator will be left in service whilst the works are carried out.
Over the following three days the new penthouse assembly and extension duct components were lifted into position onto the roof area by the tower crane and built section by section. Once constructed the tower crane lifted the materials into position to allow the engineers fit and fix into place.
On completion of the successful installation of the penthouse assembly, screen wall and new generator exhaust flue, our engineers tested the generator to monitor the air intake temperature and measure of the air flow through the inlet ensuring that it met the proposed standards and alleviated the cooling issues.
With a positive outcome of the test and successful commissioning, our engineers left behind clean and tidy premises and a very satisfied client.